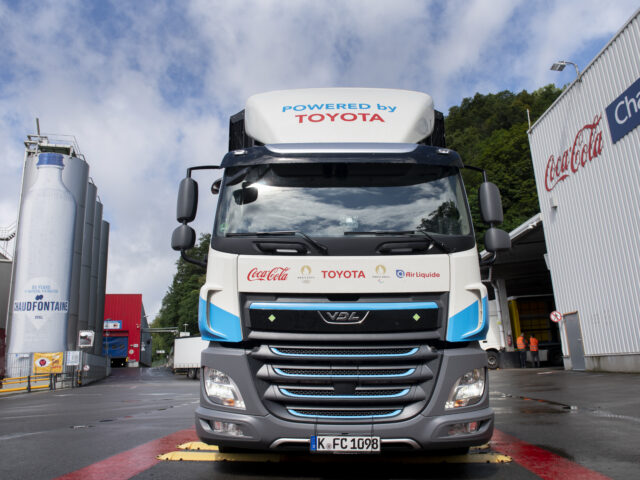
A BMW ‘i’con comes to an end: i3 production has stopped
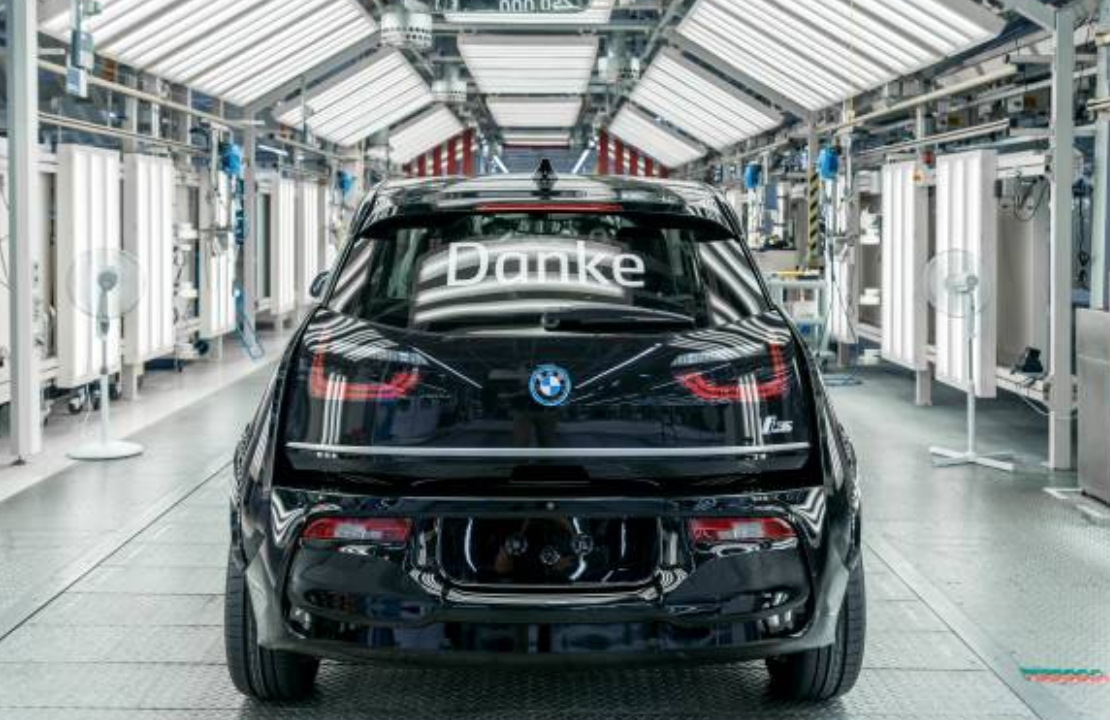
After 250 000 units produced in eight and a half years, BMW’s first fully electric car, the iconic i3, takes the bow /BMW
The 'i'conic BMW i3 ends its production with just over 250 000 units produced in the eight and a half years of its existence. It has never b
Comments
Ready to join the conversation?
You must be an active subscriber to leave a comment.
Subscribe Today