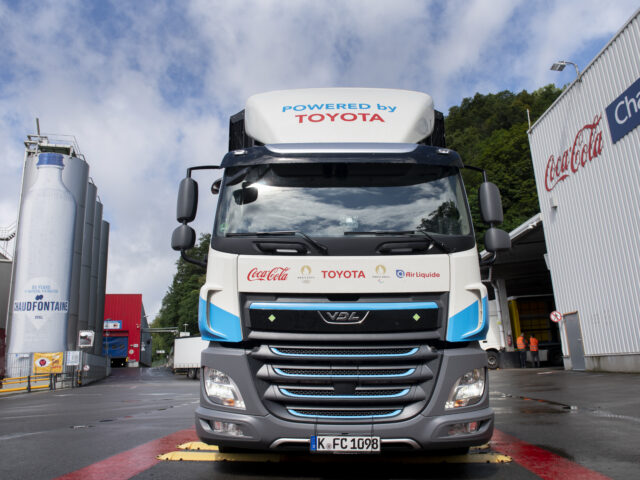
BMW Group to use innovative round battery cells from 2025
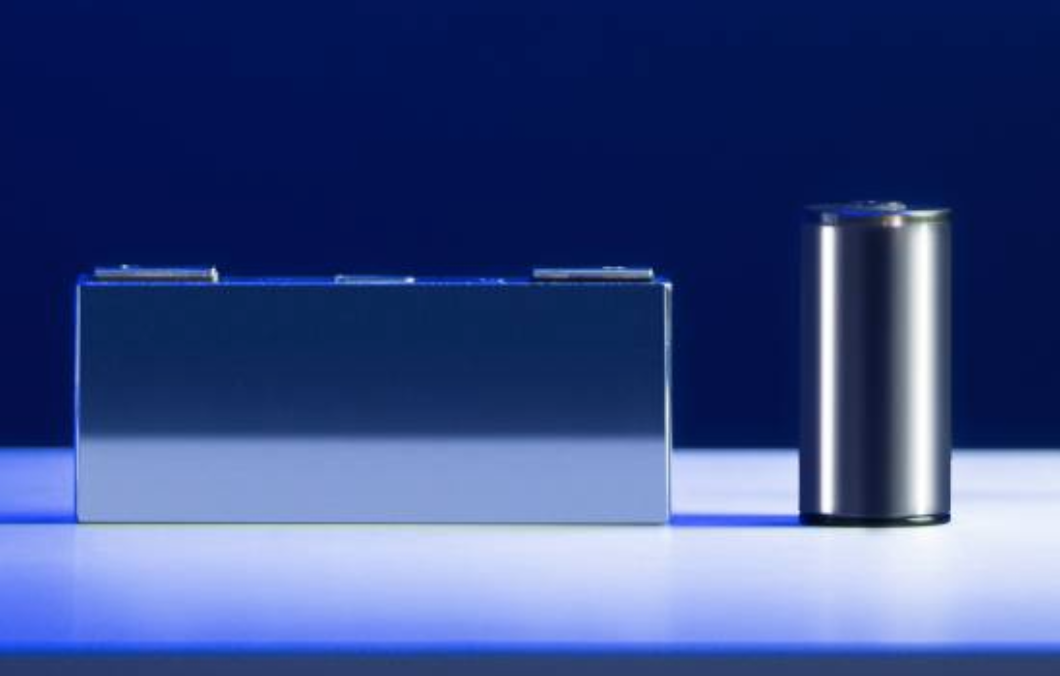
From 2025 on, BMW will use more performant round battery cells for its ‘Neue Klasse’ /BMW
The BMW Group is set to launch a new era of e-mobility from models of its 'Neumodels e Klasse' using newly-developed round battery cells opt
Comments
Ready to join the conversation?
You must be an active subscriber to leave a comment.
Subscribe Today