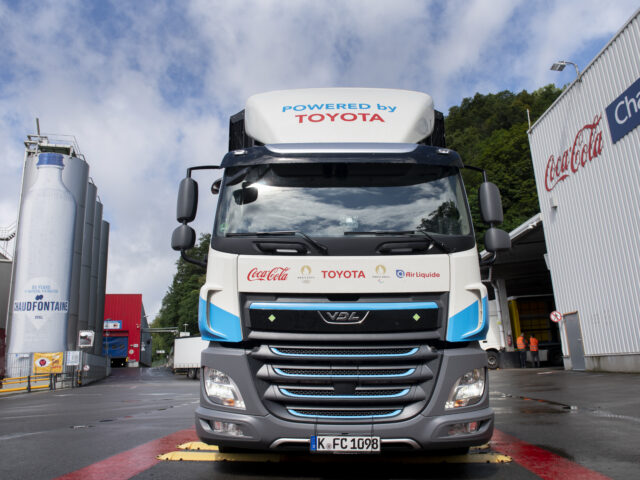
BMW bets on (at least) two horses, EV and FCEV

BMW is continuing to look into hydrogen as an alternative for BEVs and is building 100 iX5 Hydrogen vehicles to collect info on everyday usage /BMW
The BMW Group has presented plans on how to expand the capacities for EV component production. At the same time, CEO Oliver Zipse declares t
Comments
Ready to join the conversation?
You must be an active subscriber to leave a comment.
Subscribe Today