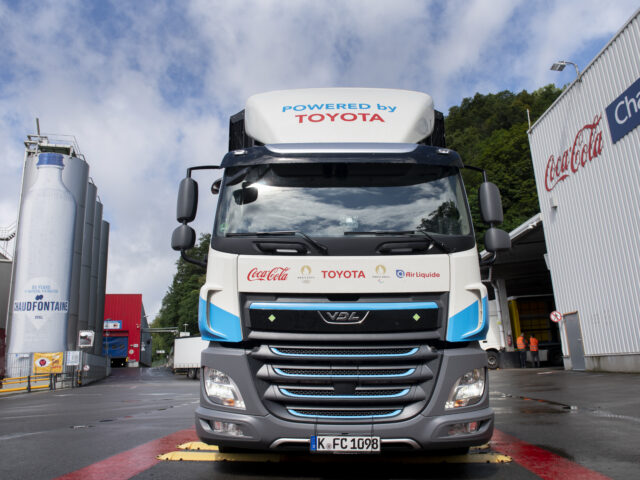
BMW prepares production of the all-electric Mini Countryman in Leipzig
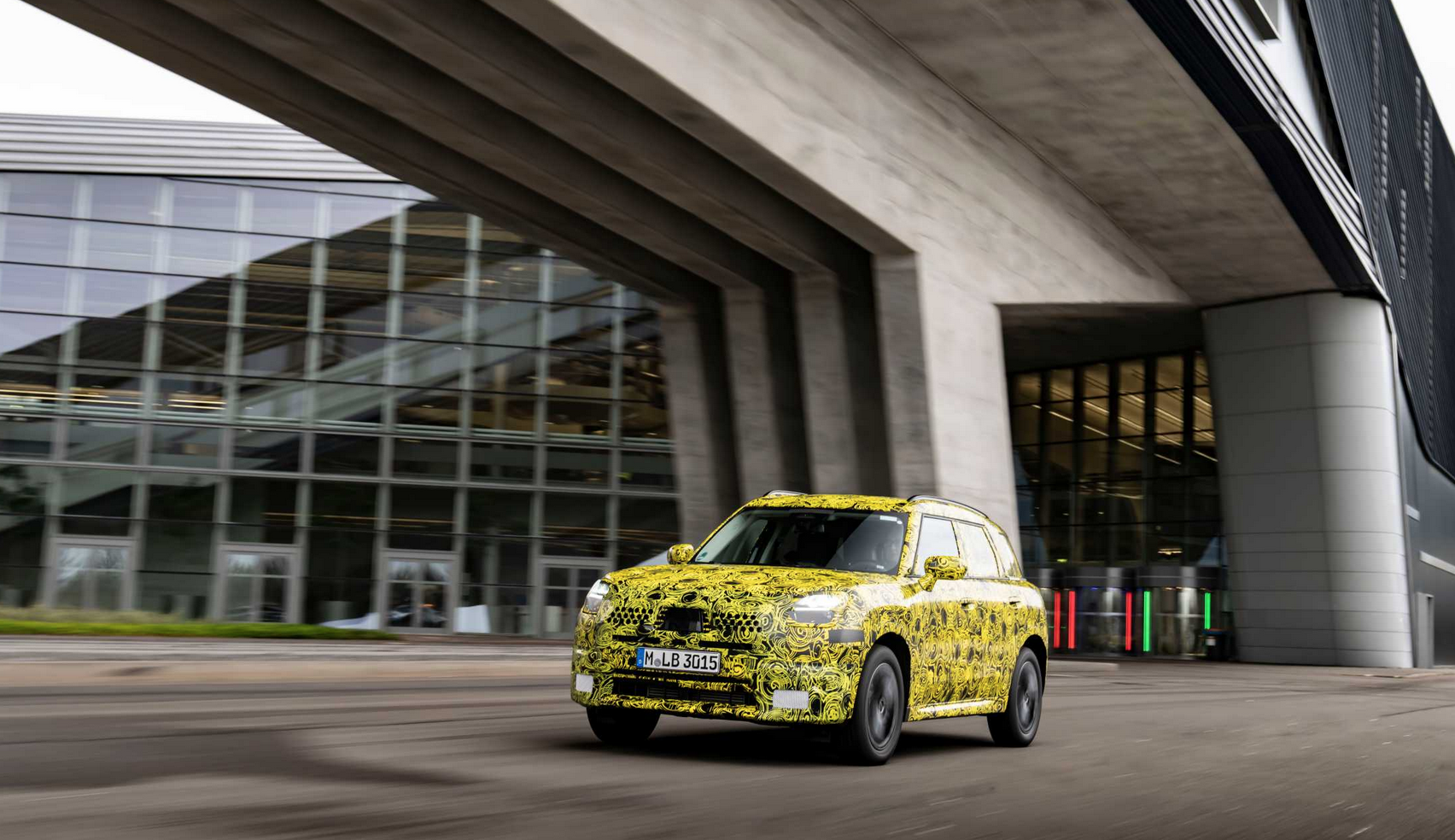
A still camouflaged test car of the new electric Countryman on the new factory premises /BMW
In 2023, the new Mini Countryman production will begin at the BMW Group plant in Leipzig. The crossover model will be offered with pure elec
Comments
Ready to join the conversation?
You must be an active subscriber to leave a comment.
Subscribe Today