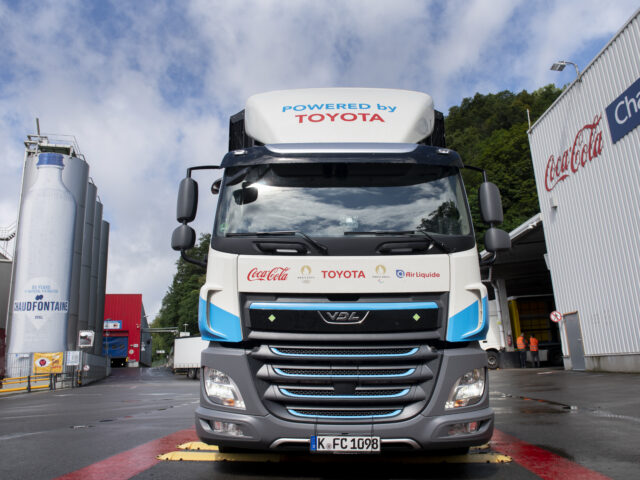
BMW produces first battery cell samples for its ‘New Class’
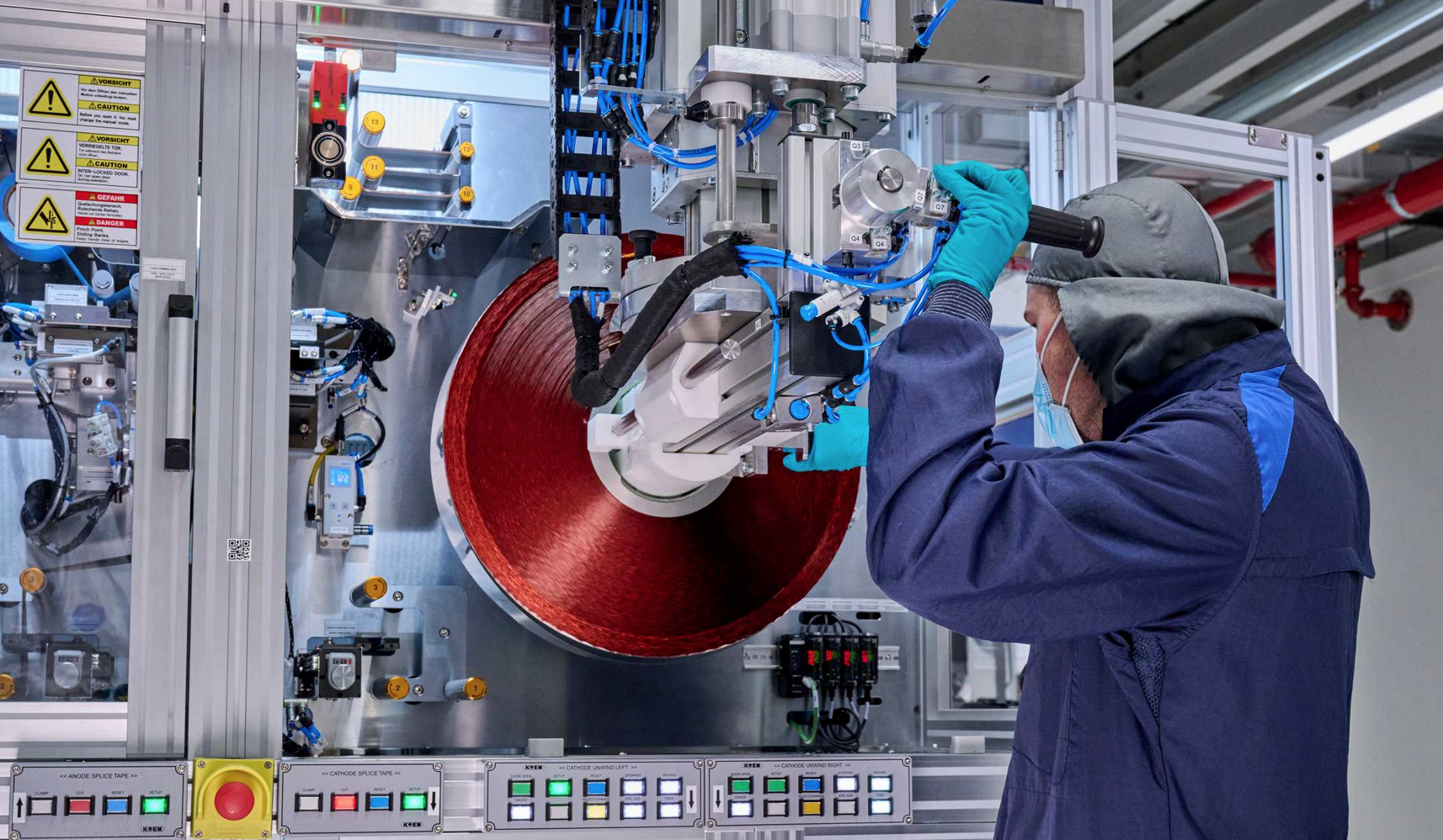
In its competence center in Parsdorf, BMW will produce cell samples for the ‘New Class’ batteries /BMW
BMW is now producing the first battery cell samples, which it will use in the New Class models from 2025. Production occurs at the manufactu
Comments
Ready to join the conversation?
You must be an active subscriber to leave a comment.
Subscribe Today