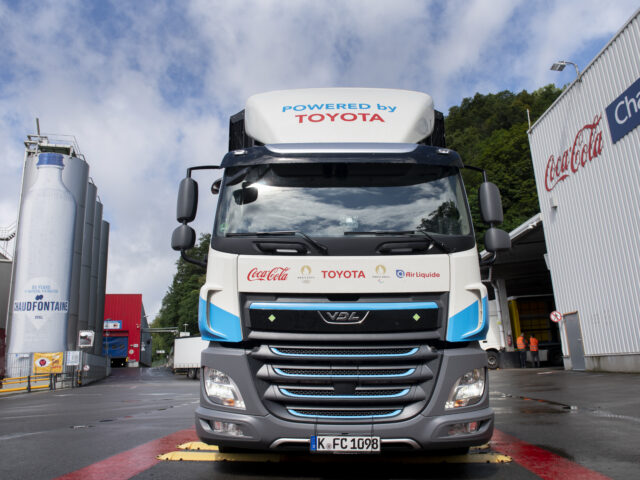
Chips shortage forces Volvo Car and Trucks to slow down again
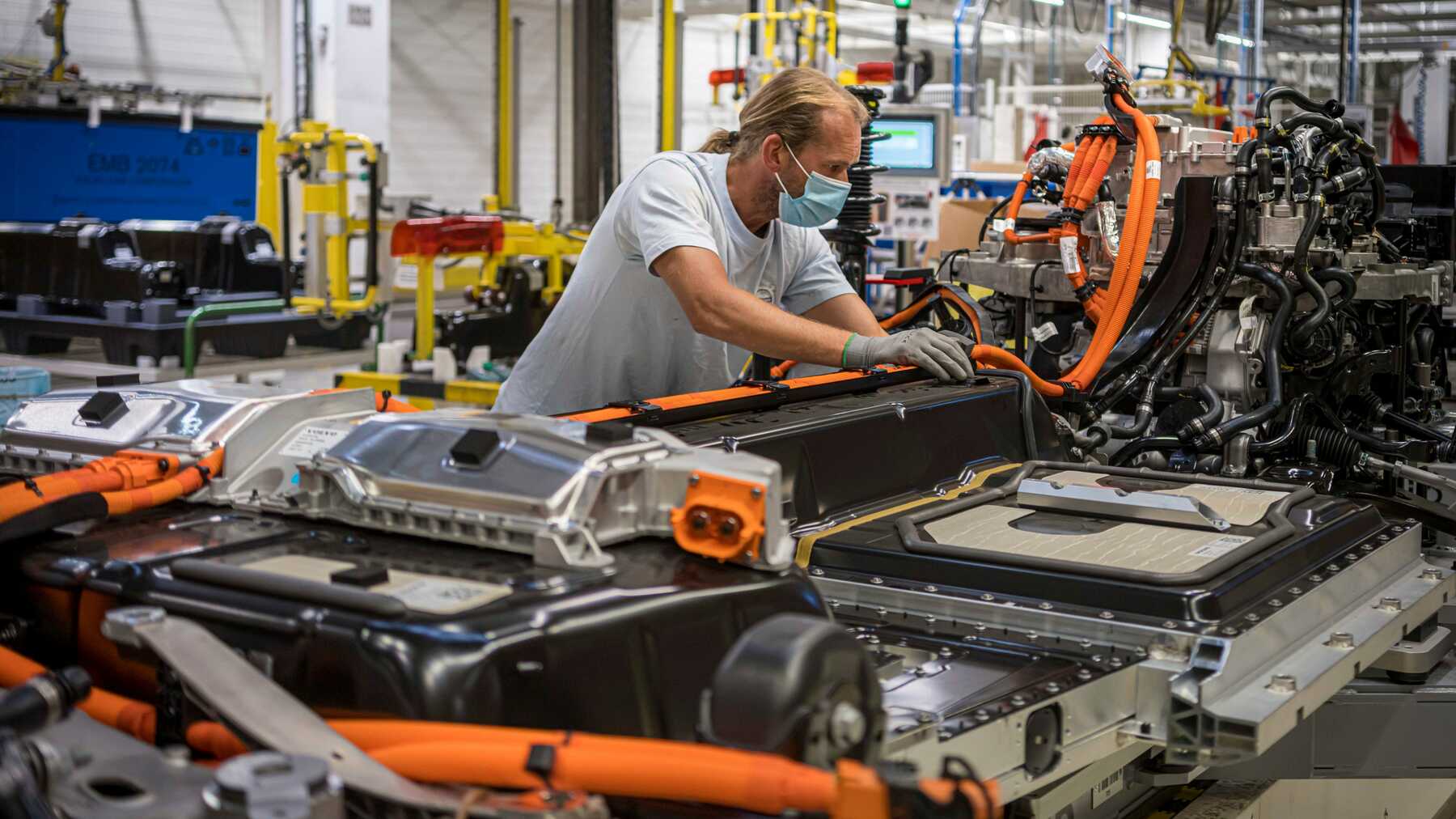
Vovo Car Gent, producing the XC40 Recharge, among others, will be forced to slow down again. In March last year, it opened a new battery assembly plant alongside /Volvo
The worldwide shortage of semiconductors forces Swedish carmaker Volvo Car again to slow down and temporarily stop production in China, the
Comments
Ready to join the conversation?
You must be an active subscriber to leave a comment.
Subscribe Today