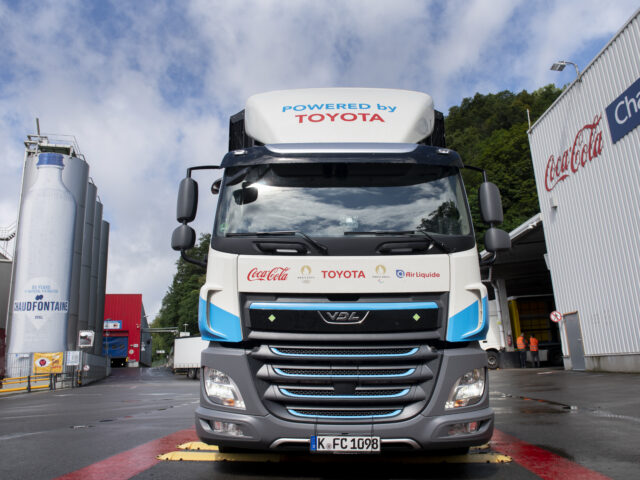
This is the world’s biggest hydrogen truck
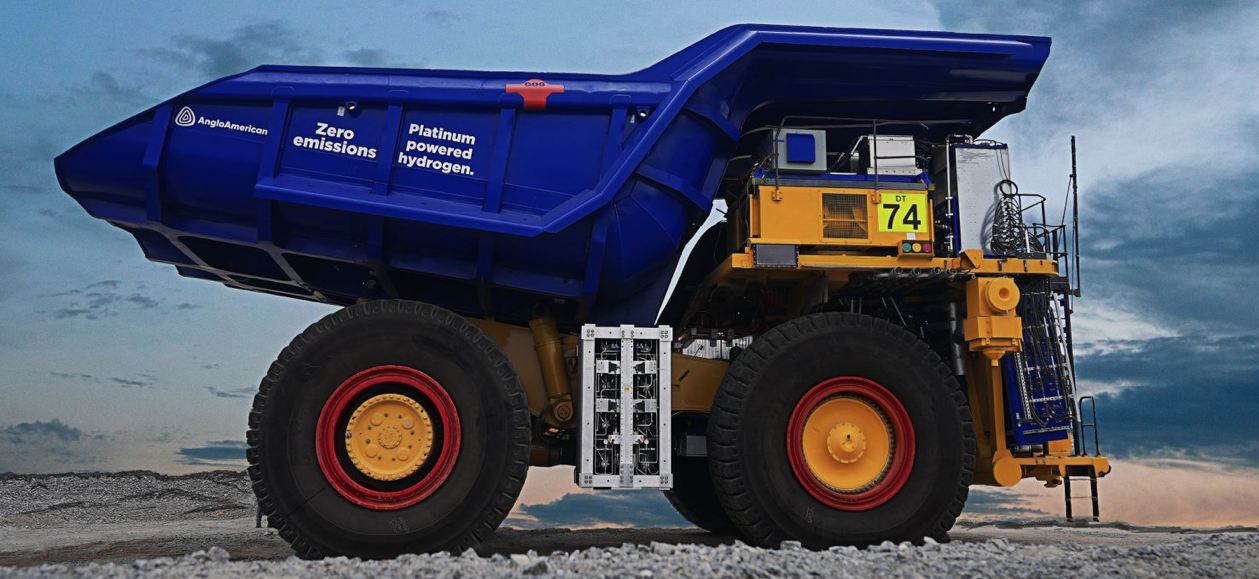
Anglo American Mining’s hydrogen hauler is more powerful than its equivalent running on diesel. The mining company wants to replace its entire fleet with hydrogen trucks. /Anglo American
Anglo-American Mining has put its first hydrogen-powered mining truck on duty. This zero-emission behemoth is poised to replace the mining g
Comments
Ready to join the conversation?
You must be an active subscriber to leave a comment.
Subscribe Today