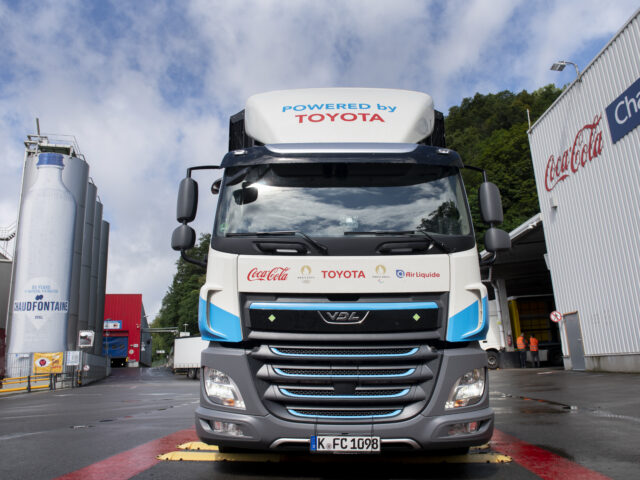
EU wants its own ores for electric motor production
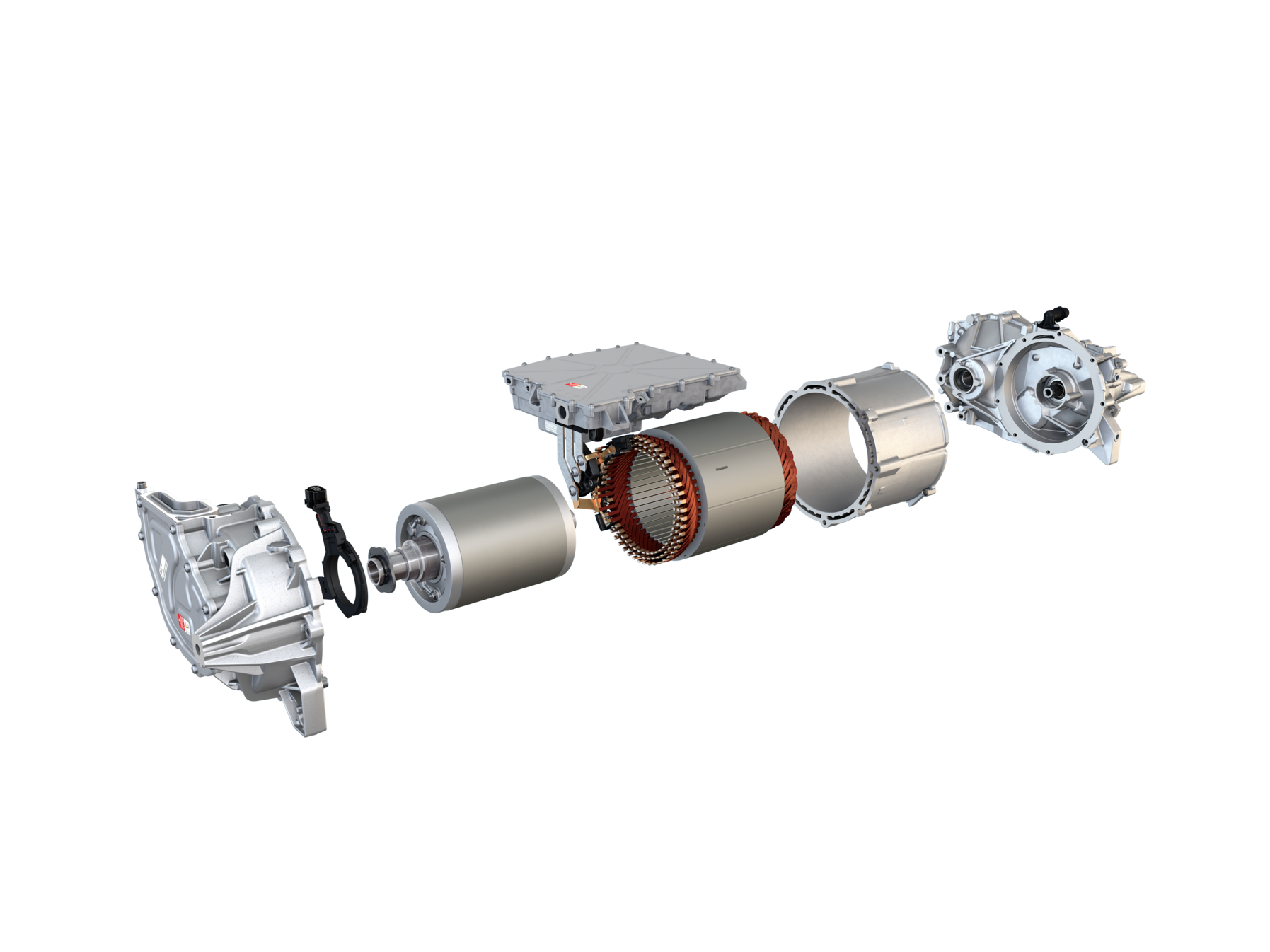
Europe is a global leader in the production of electric motors, but too dependent on foreign supply for the magnets. The new REEsilience project must change that /Volkswagen
While Europe is in a catch-up race for battery cell production, it holds a top position worldwide for producing electric motors used in elec
Comments
Ready to join the conversation?
You must be an active subscriber to leave a comment.
Subscribe Today