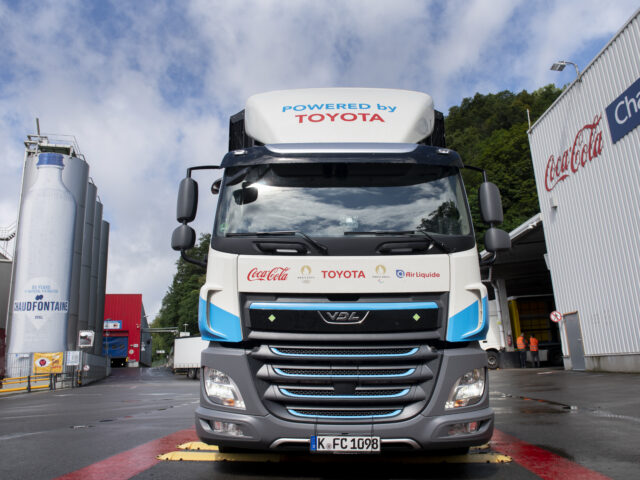
Fairbrics to transform captured CO2 into clothing polyester in Antwerp
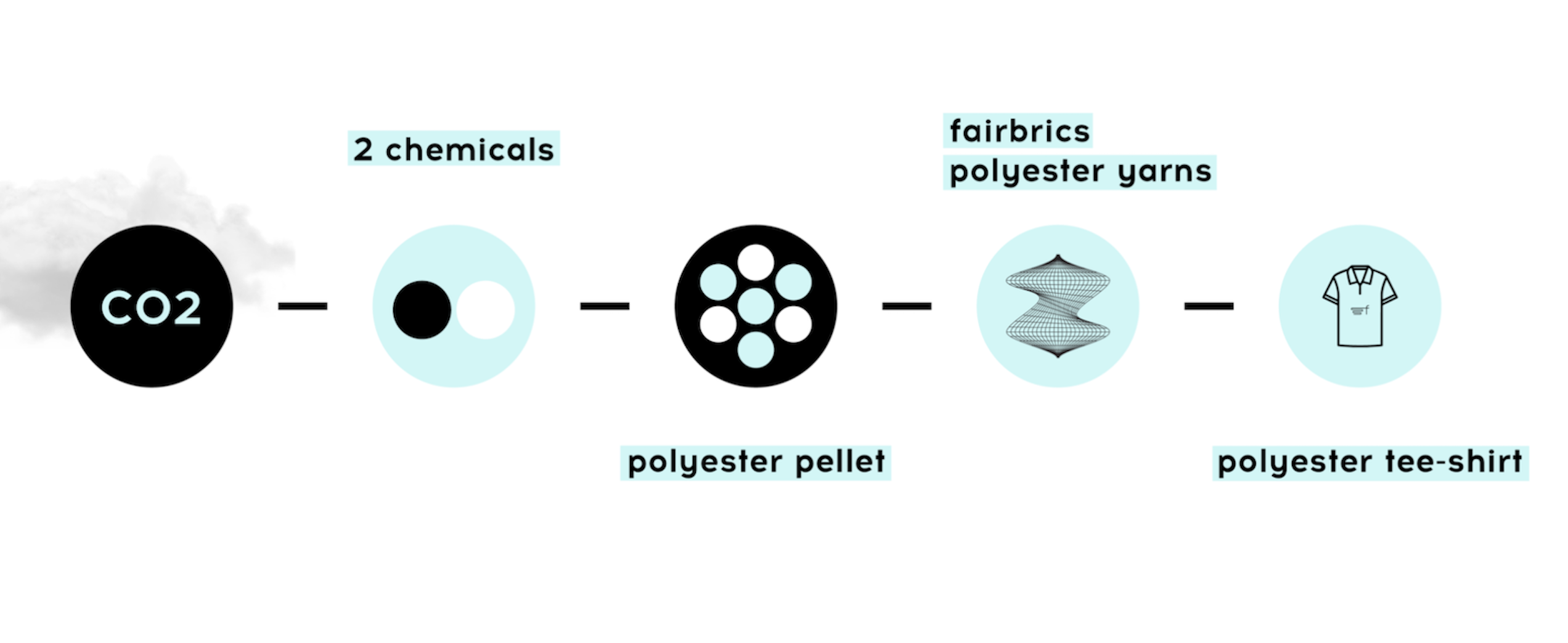
The French company Fairbrics wants to set up a pilot plant in the port of Antwerp by 2024 to capture CO2 emissions and transform them into polyester for the clothing industry /Fairbrics
The French start-up Fairbrics, a pioneer in the field, wants to capture the CO2 released by manufacturers to transform it while using molecu
Comments
Ready to join the conversation?
You must be an active subscriber to leave a comment.
Subscribe Today