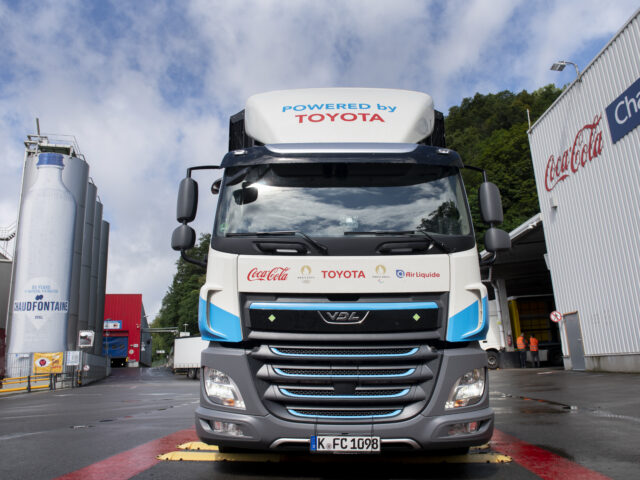
Audi optimistic about material recycling of steel
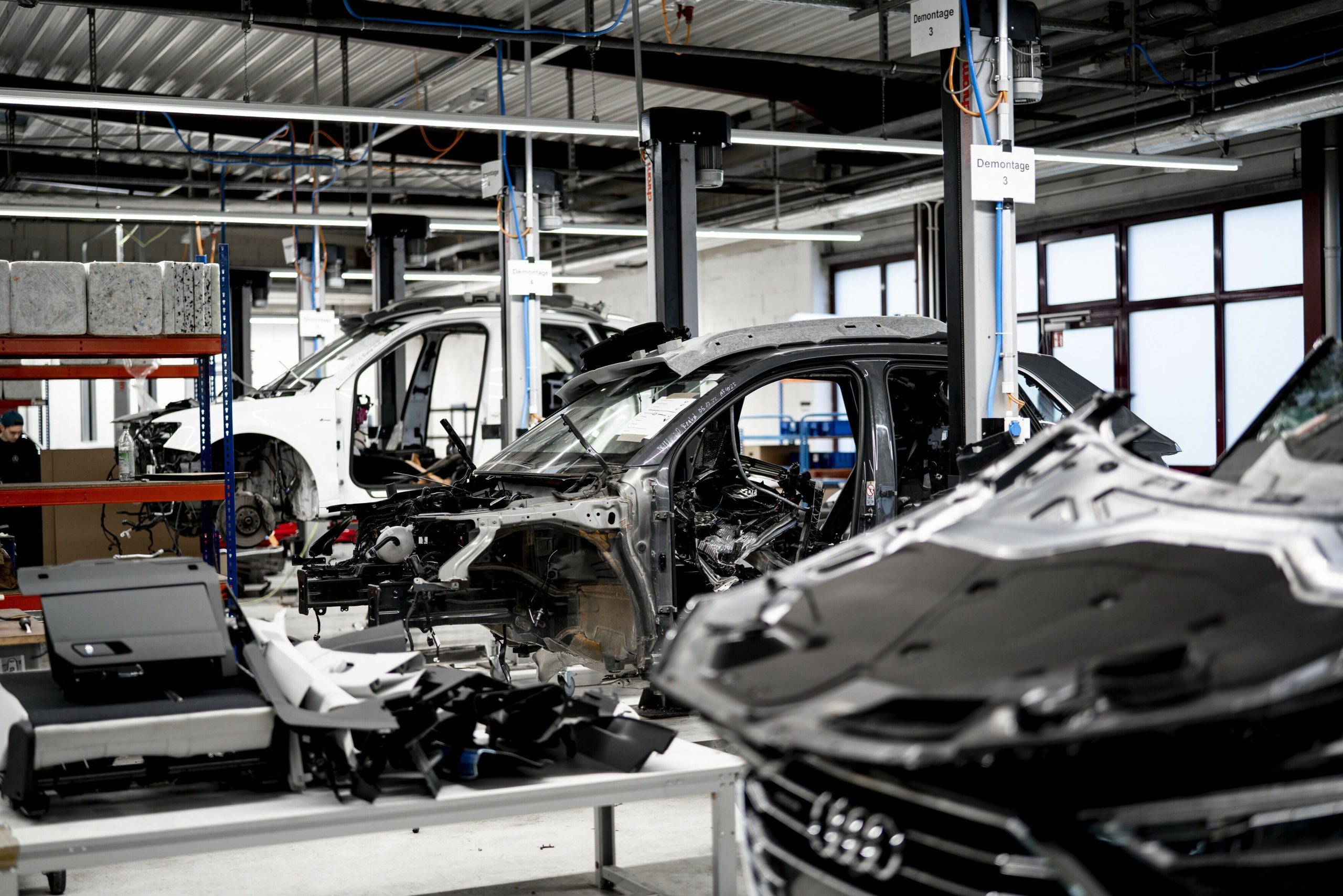
Audi”s pilot project MaterialLoop leads to interesting findings, but how will it fair when it ends in April? /Audi
Audi has released some preliminary findings of its MaterialLoop project. In the end, this must lead to a closing material cycle used in its
Comments
Ready to join the conversation?
You must be an active subscriber to leave a comment.
Subscribe Today