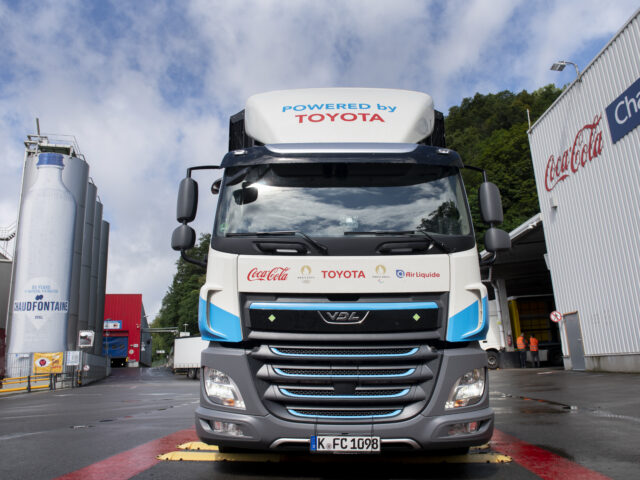
Mercedes introduces carbon-friendly aluminium on EQE and EQS
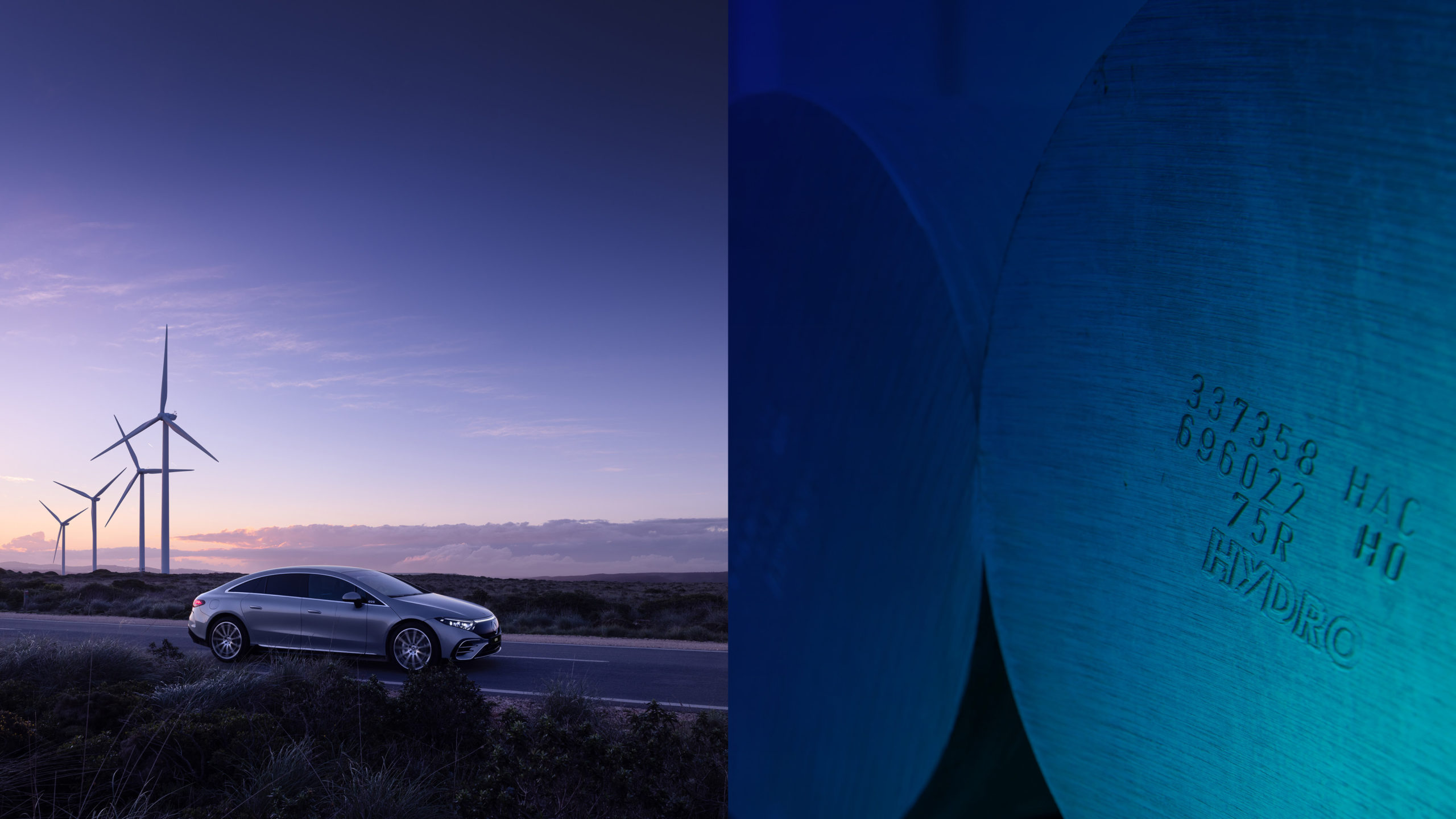
Aluminium production emits four times more CO2 than steel, but the low-carbon variant from Hydro is 70% greener. /Mercedes
Mercedes starts to manufacture the EQE and EQS models with aluminium of a significantly reduced carbon footprint as of this summer. As alumi
Comments
Ready to join the conversation?
You must be an active subscriber to leave a comment.
Subscribe Today