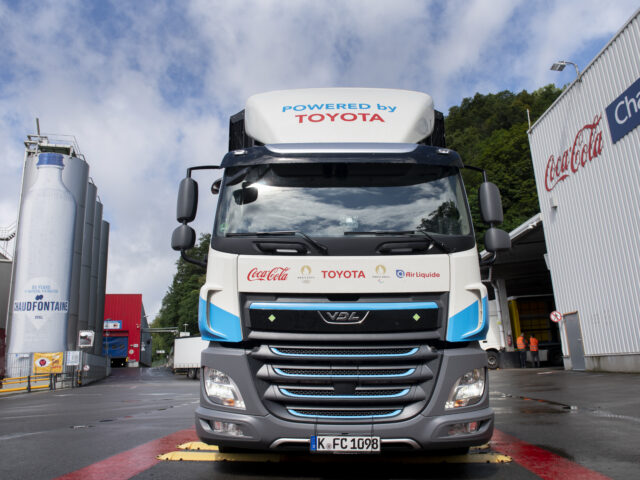
Is rhubarb a miracle technology to recycle batteries?
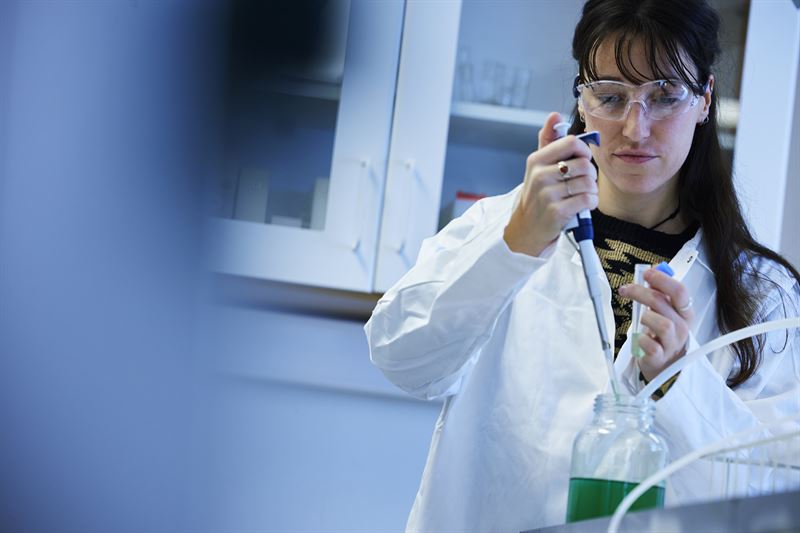
The researchers at Chalmers University use an organic acid to recycle the critical materials /Chalmers Tekniska Högskola, Henrik Sandsjö
Scientists from Chalmers University in Gothenburg have developed a breakthrough method for recycling used battery packs, not by complex and
Comments
Ready to join the conversation?
You must be an active subscriber to leave a comment.
Subscribe Today