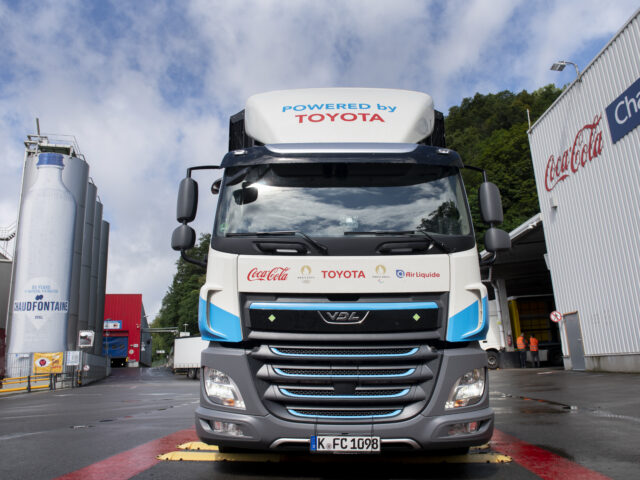
Volvo’s upcoming EX60 will be built like a Tesla
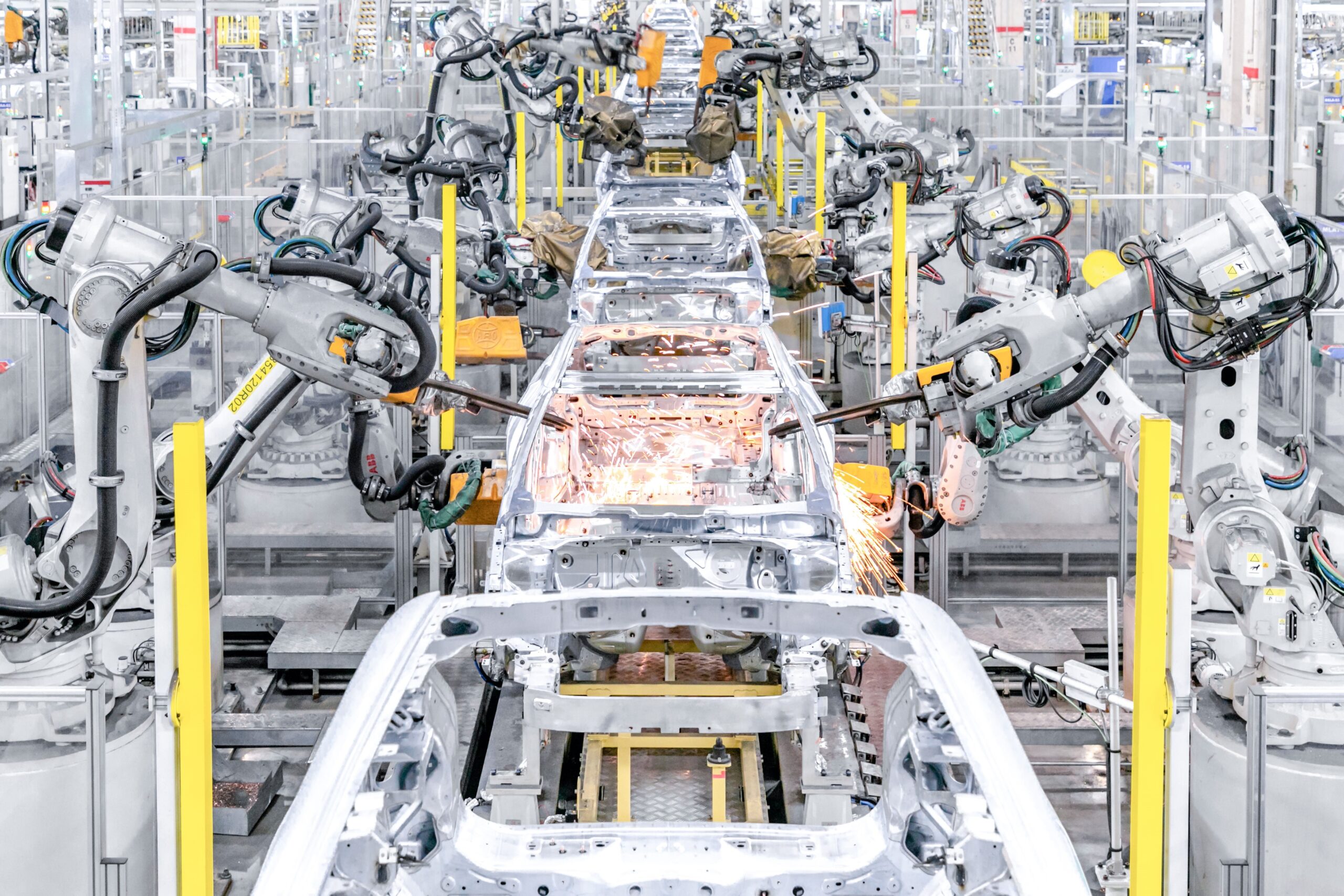
Reportedly, Volvo plans to introduce its new assembly method in 2026 /Volvo
Sticking to its deadline of an all-electric line-up by 2030, Volvo plans to overhaul its production process. Its platform for next-generatio
Comments
Ready to join the conversation?
You must be an active subscriber to leave a comment.
Subscribe Today