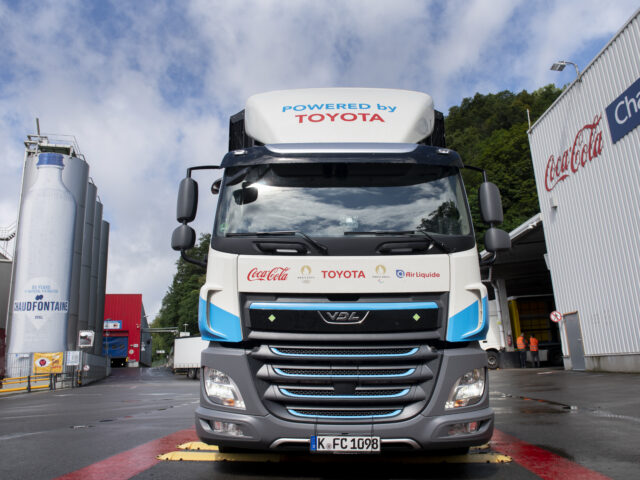
Stellantis starts testing lithium-sulfur batteries from Lyten
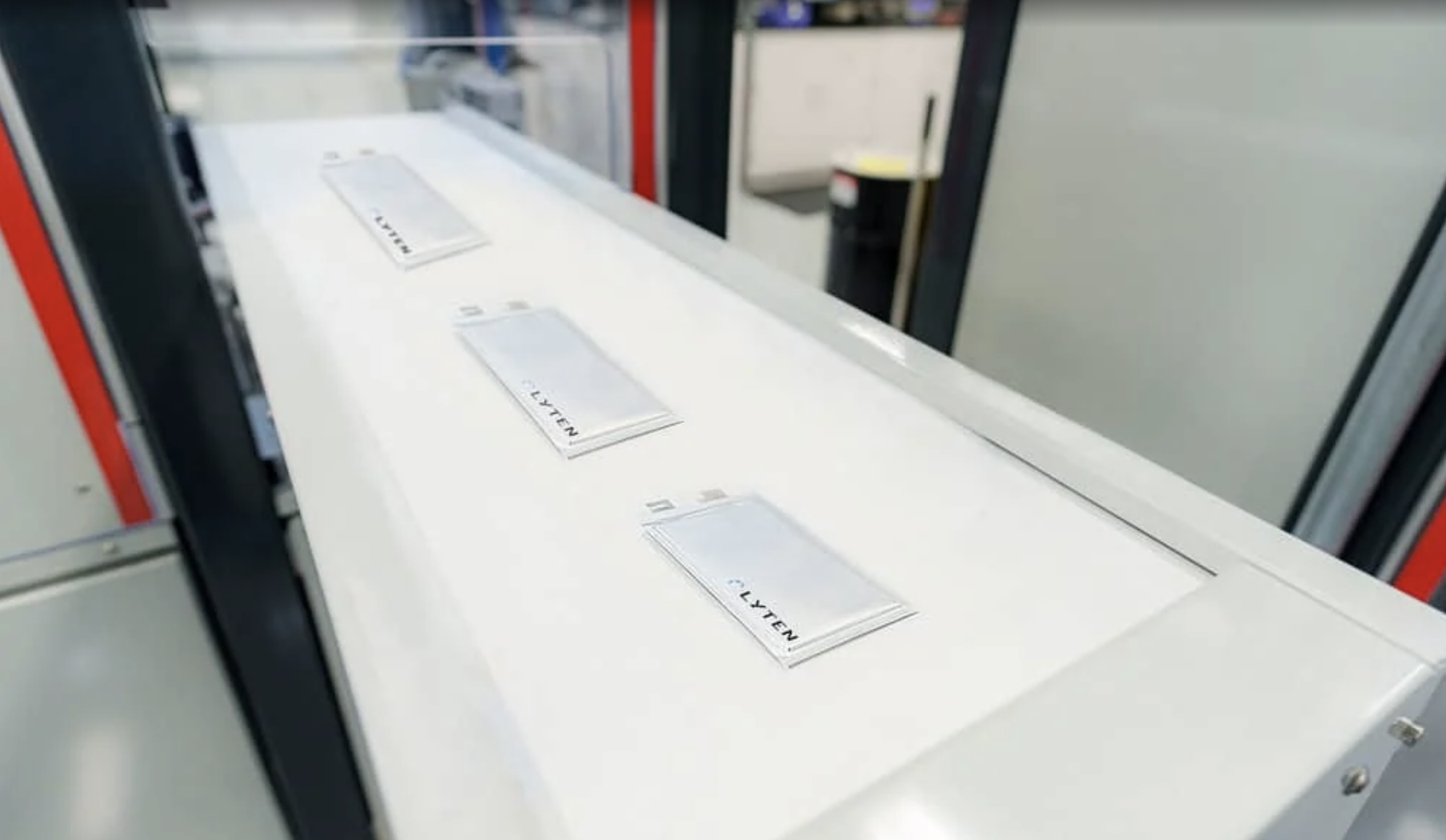
The energy density from lithium-sulfur is twice as good compared to lithium-ion /Lyten
Stellantis has received testing samples from Lyten, a start-up in lithium-sulfur battery technology that it started investing in last year.
Comments
Ready to join the conversation?
You must be an active subscriber to leave a comment.
Subscribe Today